COBRA: Robot Deflection Modeling
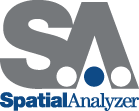
COBRA: Robot Deflection Modeling
The COBRA robot is a product of Framatome-ANP (Advanced Nuclear Power) in Lynchburg, VA.
Overview
The real-time deflection compensation method presented here was motivated by the development and refinement of the Cobra manipulator series. Framatome-ANP began development of the first Cobra manipulator in 1989. Cobra was developed to assist in the inspection and repair of nuclear power plant steam generators. The tasks performed by Cobra include eddy current inspection of steam generators, as well as repair of failed steam generator tubes via plugging, sleeving, and welding.
Cobra is a four-degree-of-freedom, all-revolute manipulator. The joints consist of high-speed (10,000 RPM) motors and harmonic drive gear reduction units (10,000:1). The second link of the manipulator includes a latching device used to break the manipulator down for transportation and installation. The manipulator is installed into a steam-generator through an 18 inch diameter access porthole, called the manway. Installation is performed using a device called the mezzanine and a removable track.
Cobra was specifically designed to operate in the Limited Access Workspace of a nuclear steam generator quarter sphere bowl. Since the manipulator was designed around its environment, the result was a relatively lightweight, portable, semi-modular manipulator.
Cobra is considerably more flexible and lightweight then common industrial manipulators. In fact, Cobra is a near worst-case scenario for deflection modeling. Cobra weighs less than 150 lb., and is capable of lifting over 100 lb. at a full extension of 6 ft. Given the high strength to weight ratio of Cobra, the stiffnesses of the links and joints are important factors in the positioning accuracy of the system. When using some of the heavier repair tools, the accuracy of Cobra is substantially degraded. In addition to the flexibility of the manipulator itself, the flexibility of the mezzanine causes significant end-effector deflections. The success of the deflection model for Cobra indicates that this model may be successfully applied to other manipulators.
The installation of Cobra into a steam generator requires first inserting the mezzanine into the steam-generator manway. After inserting the mezzanine and securing it to the manway, a track is attached to the mezzanine. Cobra is broken into two parts by releasing the latch on the second link. Next, the lower portion of the arm is attached to the track and propelled into the steam generator. Once the lower portion of Cobra is almost inside the steam generator, the rest of the manipulator is latched to the second link. The entire manipulator then travels to the end of the track where the base of the manipulator is locked to the mezzanine platform using a series of air-actuated cam devices. After touching three known calibration points in the steam-generator cavity, Cobra is ready to begin performing its inspection and delection model.
Deflection Model
The kinematic model of the manipulator was augmented with additional matrices for each link that represent the deflection of the member. These matrices model the torsion and bending of the links as a function of the load on the manipulator. The load of each link itself is accounted for as well as end loading on the end-effector. The difficult step is then to determine the proper coefficients to map the loading description to the deflection description. This is done using experimental methods.
Experimental Determination of Deflection Model Parameters
First, the end-effector is equipped with a pointing device or a sharp tool tip. The tip is driven to a fixed point in the workspace, and the manipulator joint values are recorded. A known weight is applied to the end-effector, causing the tip to move away from the touch point. The manipulator is then driven back to the same point, and the new joint values are recorded. In order to optimize the model to fit this data, the following process is used: The deflection model is given the unloaded set of joint values, and the corresponding tool position is determined. The model is then modified to include the applied load, and the new joint values. Again, the tool position is determined. The objective function contributors are the x, y, and z positional differences between the two modeled end-effector locations. When the difference is driven to near zero for all test points, the stiffness parameters are optimal.
Results
The positioning accuracy of Cobra was substantially improved by the implementation of the deflection model. Though the end-effector deflected as much as 1.5 inches due to the manipulator’s own weight, deflection compensation allowed the manipulator to perform tasks requiring a positioning accuracy of 90 mills (0.090 inches). This improvement is due in part to the increased touch-calibration accuracy. The compensation of the end-effector deflection at the goal point also contributed significantly to the positioning accuracy improvements.
Example
This example demonstrates the amount of deflection in the manipulator for a "stretched-out" configuration. In this case, a 30 lb. weight was added to the end of the tool. Note that even in a case like this with 30 lbs on the end of the arm, the deflection model allowed the manipulator to position to within 0.090 inches.
Click here to learn more about our custom applications or click here to read more about real-world SA applications.