FAQs & Glossary
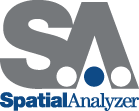
Frequently Asked Questions
- CAD Import
- Coordinate Systems
- Instrument Support
- Organization & File Management
- Traceability
- Instrument Alignment
- Watch Windows
- Inspection
- Relationships
- Standardized Inspection (GD&T)
- Thermal Scaling
- Working with Level
- Synchronized Measurement Applications (Trans-Track)
- Reporting
- Data Export
- Time Saving Tips & Tricks
- Scripting (Measurement Plans)
CAD Import
Can I import CAD? Which formats?
Yes, all SA packages include CAD import capability. Supported CAD formats include IGES, STEP, STL, CATIA®, SolidWorks®, NX®, ProEngineer®, Creo Parametric Inventor, and more. Consult the SA User Manual for a complete list.
Click here to read "How to Simplify CAD for Metrology Jobs"
Coordinate Systems
How do I define a coordinate system in SA?
SA uses the term “frame” to define a coordinate frame or coordinate system. Each frame is a complete 6 dof position in space. You can create as many frames as you would like. You can select any frame in a job file and make it the working frame or the origin of your coordinate system. The position of all objects in the job are then reported based on the working frame coordinates and are automatically updated.
How do I view/report data in different coordinate frames?
Reporting in a local part frame is handled by simply selecting that coordinate frame prior to reporting. The active coordinate frame is identified in the report for clarity.
Instrument Support
What instruments does SA support and how many can I use at the same time?
Currently, SA directly connects to more than 120 different measurement sensors and supports a wide variety of interface formats (Ethernet, Wifi, Bluetooth, SCSI, USB and RS232, to name a few). Practically speaking, there is no fundamental limit to the number of instruments that can be used simultaneously within an SA job. You can add and operate as many as you would like all at once. Your primary limitations are screen real estate and network traffic.
How do I get started measuring with a new instrument in SA?
To connect and operate an instrument in SA, just connect the instrument to the computer, add the instrument to the job file, and start the instrument interface. For more specific directions, refer to the Instrument Quick-starts located in the SA User Manual for a particular instrument.
How do I connect to multiple instruments in SA?
Click here to read "How to Simultaneously Connect to Multiple Trackers in SA"
How do I get accurate time stamps with points in SA?
Click here to read "How to Get Accurate Time Stamps with Points in SA"
Organization & File Management
How do I organize my files in SA?
Click here to read "How to Use Collections in SA"
How can I customize SA?
Click here to read "How to Customize SA"
Traceability
Are measurements traceable?
The ability to “drill down” into measurement details to find exactly what the sensor observed is fundamental to SA’s design. By recording exactly what the sensor observed, along with and separate from other measurement assumptions, questions like “was the wrong probe used,” “at what temperature was the measurement taken,” and “what points were used in the alignment,” are all answerable. Not only that, they’re usually correctable without requiring re-measurement.
Instrument Alignment
How do I align my instrument and measurements to a part?
SA provides several ways to align an instrument to a part or an object being measured. SA will guide you through measuring a set of nominal points, providing the ability to automeasure remaining points after an initial set are measured. It provides a guided 3-2-1 quick alignment to CAD option and the ability to Best-Fit a group of measured points to nominals. Point measurements are associated with the instruments that measured them, not objects, so alignment can be make before, during, or after a measurement job. Instruments can also be moved graphically and their associated measurements come along for the ride making it easy to provide an initial rough alignment or visualize measurements associated with an instrument.
How much control do I have in aligning measurements?
Weights and tolerances optionally provide additional control during alignment. In a point-to-surface fit, for example, weighting can be used to distribute the error evenly between the points (which may have been more heavily sampled on one feature) or between the features. Additionally, weighting may be automatically allocated, accounting for tolerances, such that the more critical features command higher weight.
How do I add an instrument position?
The quickest way is to simply right-click on the instrument to be moved, and choose “Jump Instrument to New Location.” This will automatically hide the old instrument, add a new instrument to the job, connect that instrument to the instrument interface, and walk you through realigning that instrument if desired. It’s as simple as that.
How do I minimize error propagation in bundling instrument locations?
One of SA’s greatest strengths is its ability to network instruments together to get the greatest possible accuracy. In addition to traditional bundling operations, SA has the ability to create a Unified Spatial Metrology Network (USMN), which utilizes instrument uncertainty calculations to build a network uncertainty model. This model provides a “weighted bundle,” creating realistic network uncertainty calculations. Using this model SA can greatly reduce error propagation associated with individual bundle operations.
Click here to read "Alignment Strategies for a Variety of Instruments & Data Types"
Click here to read "Instrument Alignment in SA -- Part 1"
Click here to read "Instrument Alignment in SA -- Part 2"
Watch Windows
What are “Watch Windows” and how do I use them?
SA uses watch windows to display live data taken from measurement devices and relationships. They may be used to compare the live position updates from an instrument to a surface, another point, the closest point, or other entities. They are as easy to create as right clicking on the object or instrument of interest and selecting “Add Watch Widow.”
Can I have more than one watch window open at the same time?
Yes. SA offers a variety of watch windows that display the probe's current location, proximity to the closest nominal point, or distance from a CAD surface. An unlimited number of watch windows can remain simultaneously open and updating at any one time. This can include a single instrument or multiple instruments.
Inspection
How do I inspect nominal geometry?
That depends upon what is of interest. A full GD&T inspection can be quickly performed with no programming. Or, without GD&T, measured positions of holes can be compared to design with a single group-to-group query. Alternatively, the hole comparison could consider errors of size, position and form, using the relationship fit and compare function.
Can I inspect without CAD?
Yes. Measurements may be collected before importing CAD, or without referencing CAD. When CAD is available, removing probe offset from measurements (or tip-compensation) is performed automatically. Without the surface normal, this becomes an important consideration, and SA offers many tools for this case as well.
Can I easily make an inspection program a user can follow?
GD&T implementation allows very quick creation of a guided inspection procedure, providing automated view zooming and “follow the bouncing dot” target illustration, with no programming. If GD&T isn’t required, SA feature checks can be used in the same method. In contrast, SA’s powerful Measurement Plan, a complete programming language, offers ultimate control of the user interface, measurement sensor control, and report generation.
Can I automate measurement process through the use of SA?
SA provides a suite of automatic measurement modes to automate daily measurement operations. These included options to drive instruments in automatic measurement of predefined points, modes to guide instrument operators in measurement of specific points or features, and auto-proximity triggering of measurements based on an assortment of user defined triggers. In addition, SA has its own intern programming language that can be used to automate nearly any operation within SA.
Click here to read "SA Toolkit Enhancements for Streamlined Inspection"
Click here to read "Top 20 Tips for Using the SA Toolkit & Instrument Toolbars"
Relationships
How can Relationships in SA help me?
Click here to read "Relationships in SA -- Part 1"
Click here to read "Relationships in SA -- Part 2"
Standardized Inspection (GD&T)
What is GD&T?
Click here to read "Introduction to GD&T in SA"
Click here to read "Understanding & Troubleshooting GD&T Alignments"
Thermal Scaling
What is the best way to scale my measurements for thermal expansion/ contraction?
SA supports many ways to analyze the effect of measuring a part at a different temperature than its design. One common practice that SA facilitates is to enter the part’s average internal temperature and its coefficient of thermal expansion when establishing a station, thereby setting a scale factor centered on the instrument (but prior to calculating the instrument’s transform).
Another similar approach is to use measurements of a scale bar which is both at the same temperature and of the same material as the part.
Yet another supported method, when the part reference system has been established at design conditions, is to “let scale float” and calculate it as another degree of freedom during the fit. Another unique situation that SA considers is a non-isotropic scale factor, such as a steel optical table with zerodur components. Which method is best, of course, depends on situation and shop practice.
Click here to read "Temperature Compensations in SA"
Working with Level
How can I hold level in SA?
Click here to read "Holding Level in SA"
Synchronized Measurement Applications (Trans-Track)
How do I use Trans-Track in SA for real time alignment applications?
Click here to read "How to Use Trans-Track in SA"
Reporting
How can I report my findings to a customer?
SA offers a range of reporting methods, from quick and simple to powerfully robust. The newest of which, dynamic report, is a WYSIWYG canvas supporting drag and drop, color, and font controls. Alternatively, a single click produces a composite quick report of the entire job. Additionally, reports can be exported to, or directly produced in Microsoft Excel or Adobe PDF.
Click here to read "Reporting Options in SA"
Data Export
What CAD formats can I export?
SA offers CAD Export in the vendor-neutral STEP and IGES formats as well as AIMS, SAT, VDA, and Autocad DXF. Also included is the ability to export STL files as well as to Polyworks and Imageware.
Time Saving Tips & Tricks
How can I learn time-saving tricks that will help me use SA?
Click here to read "How to Customize SA"
Click here to read "Top 20 Time-Saving Tips for SA Users"
Click here to read "Auto Measure in SA"
Click here to read "Top 20 Tips for SA Users"
Click here to read "Helpful Hints for SA Users, May 2012"
Click here to read "Helpful Hints for SA Users, February 2012"
Scripting (Measurement Plans)
How can I learn to create Measurement Plans in SA?
Click here to read "Foundations of Measurement Plans"
Click here to read "Building an MP"
Questions? Contact us at support@kinematics.com for further information or assistance.