TWS Robot Software
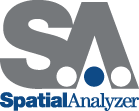
TWS Robot Software
New River Kinematics (NRK) received the software contract for the Trans World System robot from Framatome-ANP in Lynchburg, VA. FTI developed the TWS robot system as the next-generation nuclear reactor vessel inspection manipulator.
The TWS software was a complete, ground-up, custom software development effort. The goal was to produce a package capable of controlling the robot, providing meaningful user interface, and dealing with all the complexities of scanning, calibrating, and synchronizing the robot with the UT weld inspection tool. Functionality includes:
- Forward and Inverse Kinematics
- Deflection compensation
- Scan Path Planning (U, V, W, Ru, Rv, Rw motion)
- Trajectory Generation
- Interface to robot controller
- Intrinsic kinematic calibration
- Extrinsic calibration (using a vision system)
- Tool-head video image calibration
- STEP CAD format interface for vessel and environment as well as individual manipulator components
- Ability to view 2 robots in action simultaneously
- Remote monitoring of another TWS station
- Collision detection Multi-lingual user interface
- Real-time trajectory adjustment in the surface direction. This will allow the UT transducer compression to servo the controller to adjust for model versus real-world discrepancies.
Click here to view the video.
Click here to learn more about our custom applications or click here to read more about real-world SA applications.